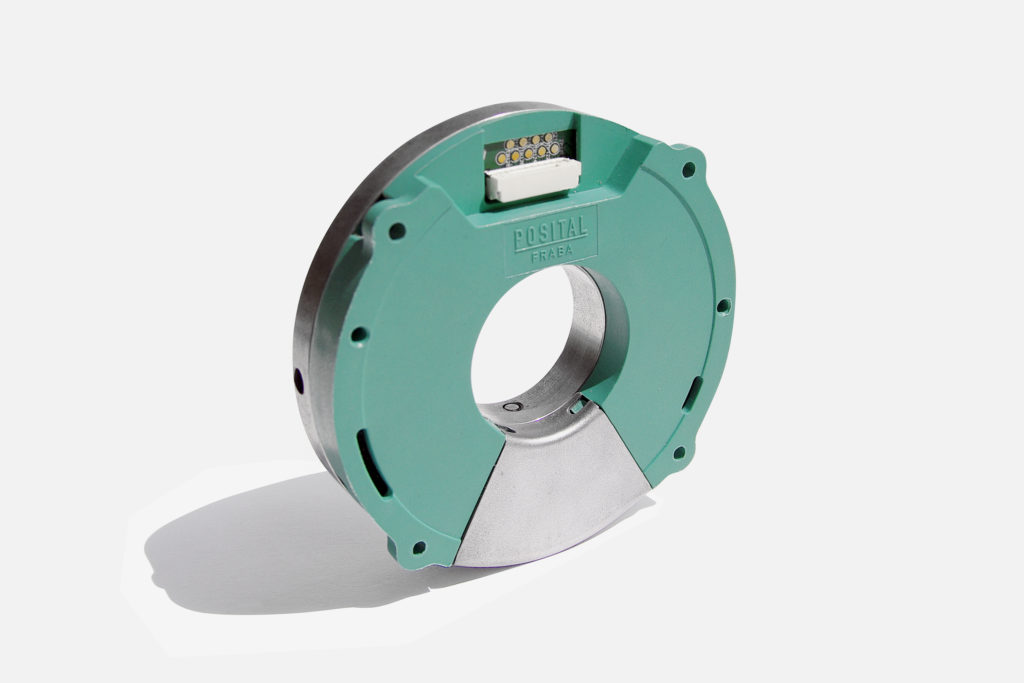
Space and power are always at a premium for robotics designers and suppliers. Although current controllers often require two single-turn encoders working in parallel, as well as a gearbox for synchronization, POSITAL FRABA’s new hollow shaft kit encoder can do this on its own.
Hollow shaft encoders, which feature a ring-shaped, open-center design, can be very useful in robots, where they can be installed directly inside joints to measure arm positions. Most hollow shaft encoders were single-turn devices, according to Cologne, Germany-based POSITAL FRABA.
The controls and sensor manufacturer claimed that it has overcome this limitation with its new capacitive hollow shaft kit encoders. They incorporate an integrated rotation counter that records every single revolution — without any need for external power supply, maintenance-prone batteries or complex gears, according to POSITAL.
This self-sufficiency is made possible by a Wiegand energy-harvesting system that POSITAL has offered for years in its conventional and kit encoders. The technology, which converts rotational motion into electrical impulses, has been adapted to the hollow-shaft design.
Hollow shaft encoders can also be very useful for servomotors, drives, and other rotating machines since their ring-shaped form factor makes them easy to install around shafts, said the company.
Hollow shaft kit intended for easy robot installation
POSITAL FRABA said that its hollow shaft kit encoders are ideal for robotics, from six-axis industrial robots to lighter and more agile collaborative robots.
The hollow shaft kits can be installed directly inside joints to monitor and control the three-dimensional movements of robot arms. Such applications demand very high levels of precision — modern industrial robots work with repeatability accuracies as fine as 0.1 mm.
For both cobots and traditional articulated robots, the central bore of the hollow shaft kits (30 or 50 mm) is available to route cables and media hoses inside the housing.
The slim design — a depth of only 17.8 mm, an outer diameter of 80 mm, and a weight of only 110 g — facilitates easy installation, said POSITAL. Only a few simple steps and screws are sufficient, it said. These devices also have a self-calibration capability that ensures accurate results with minimum setup time.

The hollow shaft kit encoder is designed for both industrial robots and cobot arms. Source: POSITAL
The capacitive measurement alternative
While POSITAL FRABA has been a leader in the migration from optical to magnetic encoder technology, it said it chose another path for its hollow shaft series. Since magnetic systems are difficult to implement in hollow shaft designs, capacitive measurement technology was the preferred alternative.
Capacitive encoders are made up of rotor and stator components, both shaped like flattened rings with specially patterned conductive surfaces that function as capacitor plates. As the rotor turns, these surfaces change their relative positions, altering the capacitive coupling across the system. This modulates the amplitude and phase angle of high-frequency electrical signals transmitted through the capacitor system.
These signal variations are captured by special ASIC processors and decoded to determine the rotor’s angular position to a high level of accuracy. The measurements are transmitted to the central controller via open-source SSI or BiSS C interfaces. Capacitance is averaged around the full circumference of the ring-shaped rotor and stator components so that the system is relatively immune to minor alignment errors or the presence of moisture or dust.
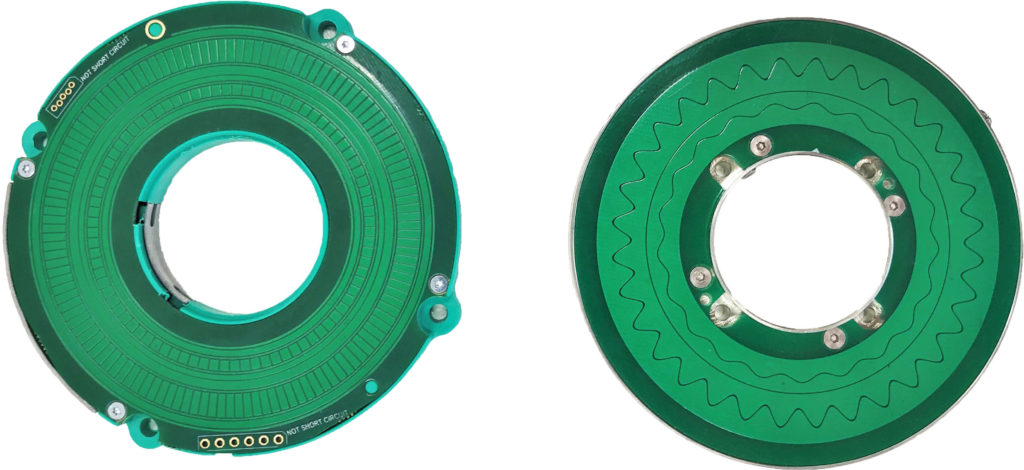
The key to the multiturn system is a special energy harvester, based on the Wiegand effect. Mechanical motion is captured as magnetic energy in a Wiegand wire, then released as a pulse of electricity to power the rotation counter. While traditional Wiegand harvesters rely on a permanent magnet mounted on the centerline of a drive shaft, a completely new setup had to be found for the hollow shaft design.
The arrangement of four permanent magnets mounted on the circumference of the rotor was developed in POSITAL FRABA’s research and development center in Aachen, Germany, through over a year’s worth of field tests and intensive magnetic field simulation.
These magnets create a stable magnetic field that the Wiegand sensor installed in the stator can detect and use. With every 360° rotation of the magnets on the rotor, a tiny Wiegand wire embedded in a copper coil generates a pulse of electric current that activates counting electronics, precisely recording every revolution. The multi-turn counter has a 43-bit memory that provides a measuring range of almost nine trillion revolutions.
‘Wiegand effect’ enables energy harvesting
Energy-harvesting components collect the electricity they need directly from their surroundings. The result is energy self-sufficiency – maintenance-free and without batteries. This topic has clearly gained momentum through Industrial Internet of Things (IIoT) or Industry 4.0 setups, which involve gigantic networks of sensors and actuators that need to be as self-sufficient as possible.
While piezo systems, thermal and kinetic processes have long set the pace for energy harvesting, the Wiegand effect, named after the U.S. inventor John Wiegand, is still considered an exotic alternative, noted POSITAL.
The core of the Wiegand system, which was patented back in 1972, is a short length of specially conditioned Vicalloy wire. At the end of a complex manufacturing process, involving cold forming and tempering, the wire emerges with a soft magnetic core surrounded by a magnetically hard layer.
POSITAL said that a special feature of this combination is that when the Wiegand wire is exposed to a changing external magnetic field, the magnetic polarity of the wire will abruptly “flip.” When this happens, a pulse of electric current is generated in a fine copper coil wrapped around the wire.
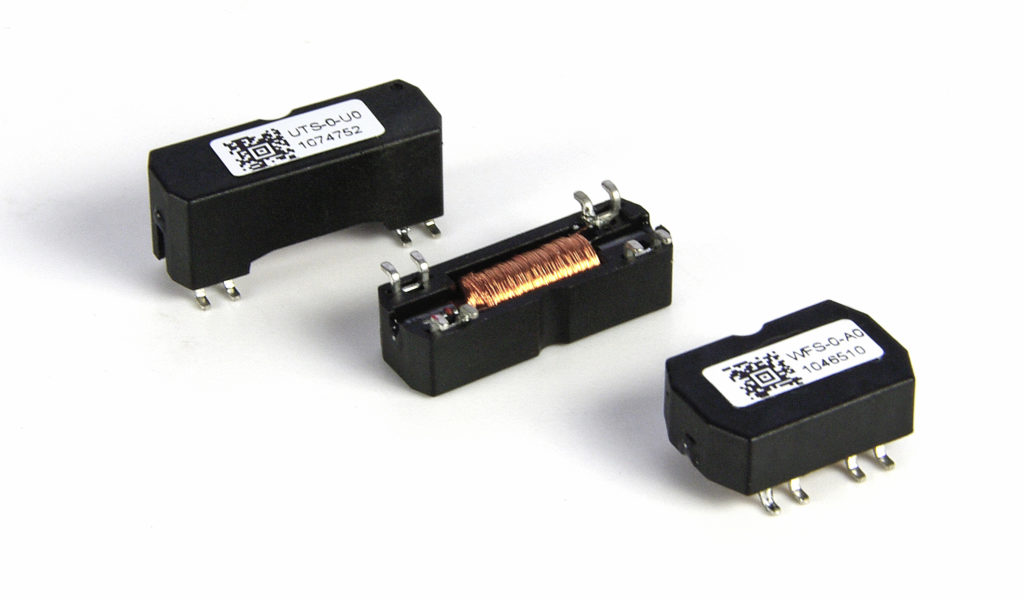
POSITAL has been using this technology since 2005, using Wiegand sensors as power sources for electronic rotation counters in the company’s magnetic multiturn encoders. The decisive factor for this breakthrough in energy harvesting was the availability of ultra-efficient low-power chips.
The Wiegand effect is pure energy harvesting, claimed the company. The magnetically induced energy comes directly from the rotary motion. Unlike a dynamo, energy is produced at consistent levels, even with very slow movements. The “mini power plants” are only 15 mm long but yield of 7 V or 190 nJ of energy — enough to reliably activate modern rotation counters and associated electronics.
POSITAL said produces 1 million compact Wiegand modules annually for commercial use. These consist of a short length of wire surrounded by a fine copper wire coil, mounted an SMD framework.
POSITAL FRAABA said it is working on increasing the energy yield of the Wiegand sensors for other applications. Tests at the R&D center in Aachen are currently reaching 10 V selectively. This could approach power levels that would enable wireless communication or radio solutions with ultra-low-power electronics, said the company.