One of the top technology news items this week was the successful launch of the Mars 2020 mission. Robotics applications on Earth are already benefiting from advances, as maxon precision motors announced the availability of its new Gear Planetary X-Series Ultra Performance, or GPX UP, product family. The company said the selectable planetary gear type for configurable X-drive assemblies will complement its existing gearhead offerings.
From the Perseverance Mars Rover to race cars, maxon credited the aerospace and automotive industries with presenting demanding design challenges that pushed it to develop viable solutions. The result is the GPX UP planetary gearbox, said the company, which is the U.S. unit of maxon motor ag. It outlined the series:
- GPX A (metal planetary pins – standard)
- GPX C (ceramic planetary pins – increased torque and life)
- GPX LN (reduced noise)
- GPX LZ (reduced back-lash)
- GPX HP (high power – increased torque capacity)
- GPX UP (Ultra performance – smooth back-drivability & maximum efficiency)
Mars mission, Formula 1 inspire extreme gearbox design
Initially, maxon developed the UP designs for the European Space Agency’s ExoMars project and NASA’s Mars 2020 mission, which launched this week. These rovers required extreme torque and power, as well as the highest efficiency possible for a lifetime of use while being exposed to extreme environmental conditions.

Cutaway of the GPX 22UP; note needle bearings between steel pins and ID of planet gears in the two upper cross-sectioned gears. Source: maxon
In addition, the GPX UP incorporates technological advances from Formula 1 racing, which also places extreme application requirements on gearbox design. One advantage of the new gearbox design is its high efficiency, or the ratio of output power/input power, according to maxon. Significantly reducing the friction in any mechanical system naturally leads to an optimized overall drive system, it said.
In a traditional planetary gear, the planet wheels/gears rotate on greased steel or ceramic pins — a simple plain bearing. However, in the UP gearbox construction, this frictional interface is replaced with needle bearings. This innovation transitions the planet gear-to-pin contacting surfaces from “sliding friction” to superior “rolling friction,” said maxon. The result is planetary wheels that rotate on smooth-running bearings increasing efficiency, dramatically lowering generated frictional heat energy and prolonging lubricant life.
The maximum efficiency of the GPX UP, which has three-stage construction, is approximately 90% in comparison with a standard gearhead and equivalent gear ratio, which only achieves ~70%, maxon said. This provides an efficiency gain of ~20%.

Efficiency vs. torque curve for GPS 32UP (solid) vs. GPS 32 standard construction (dotted). Source: maxon
If the same motor and controller are affixed to the UP gearbox, the gearbox assembly can produce 30% more torque and power at output than a traditional planetary gearbox. The same output power will require 23% less input power from the drive, said maxon. As a result of the reduced input torque need, a brushed motor is less taxed and worn, which equates to a longer lasting brush system and overall greater lifetime of the motor, claimed maxon.
In addition, this can allow a motor to operate in a more efficient area of the efficiency versus torque curve, or it can allow use of a smaller/lighter motor and associated control electronics, said the company. This can be an advantage to both weight and cost. With improved gearbox and motor efficiency, the entire assembly allows for longer battery runtimes

The 4X planetary gears with needle bearings placed in their internal diameters, unlike plain bearings, originally designed for a space application. Source: maxon
GPX UP designed for longer life
Significantly longer gearhead life is possible with the UP mainly because of the dramatically reduced friction between the planetary wheel ID and axle it rides on, said maxon.
At the same time, heat generation from operating the gear is noticeably reduced because there is less heat friction being created and emitted. The GPX UP is especially suitable for applications where temperatures should not exceed a certain threshold level — such as medical hand pieces, according to the company.
The longevity of the lubricant plays an important role in terms of wear and tear on the gearhead’s mechanical components. The greater the thermal stress, the more quickly the lubricating properties are lost. This is quickly followed by abrasive behaviors in the mechanical system. The abraded metal particles lead to agglutination of the lubricant, potentially resulting in a breakdown in its lubricating ability. In the GPX UP, the frictional interfaces are replaced with bearings minimizing generated heat.
In turn, the lubricant is kept healthy, and the life of the gearbox is tested to be 11 times greater than comparable competitor models.
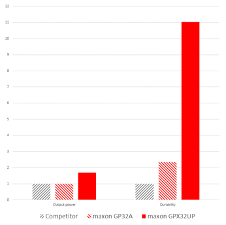
Chart of continuous power output capability and service life. Source: maxon
Not only can the GPX UP improve output specifications over traditional planetary designs, but it can also provide a viable solution to haptic or force-feedback applications, maxon said. The incorporation of needle bearings in the design can provide high efficiency, and smooth-turning planet gears are ideal for applications that require smooth and repeatable back-drivability or turning the shaft from the output side of the gearbox, it said.
The torque feedback provided thru the GPX UP to the motor on the input side of the gear is consistently proportional to the load and quantifiable. Traditionally-built planetary gearheads cannot guarantee smooth back-drivability or consistent load interpretation through the gearbox because of fluctuating efficiency, altering tolerance stack-ups within internals of the gearbox (gearbox to gearbox), and potentially cocking planet gears. The UP resolves all these issues, stated maxon.
Motor enables haptic feedback
In electronic flight control or “fly by wire,” the pilot’s steering movements are not transferred to conventional mechanical or hydraulic actuators but are transmitted electronically. The essential varying force feedback or “feel” is provided by a motor assembly in the control column of the joystick. This haptic generating motor assembly must contain a gearbox capable of both smooth back drivability and simultaneously generating torque/force based on the position of the joystick.
A similar approach is employed in cutting-edge surgical robots performing minimally invasive, micro-, and tele-surgeries. Here, it is critical that the surgeon dynamically feels instantaneous equivalent forces as they are being exerted by the robot performing the procedure some distance away.
The criticality of a smooth back-driving gearbox within the motor assemblies for both the surgeon and surgery robotic consoles cannot be overemphasized. The GPX UP delivers this functionality, even for gear ratios requiring two or three planetary stages.
A traditional gear that has uneven or “sticking” back drivability is unusable and introduces noise to the mechanical system. The UP is an optimized haptic gearbox where torque cleanly passes through the gearbox either from the input or output sides of the gearbox, resulting in a superior haptic experience, mechanical system, and overall surgical robot, said maxon.
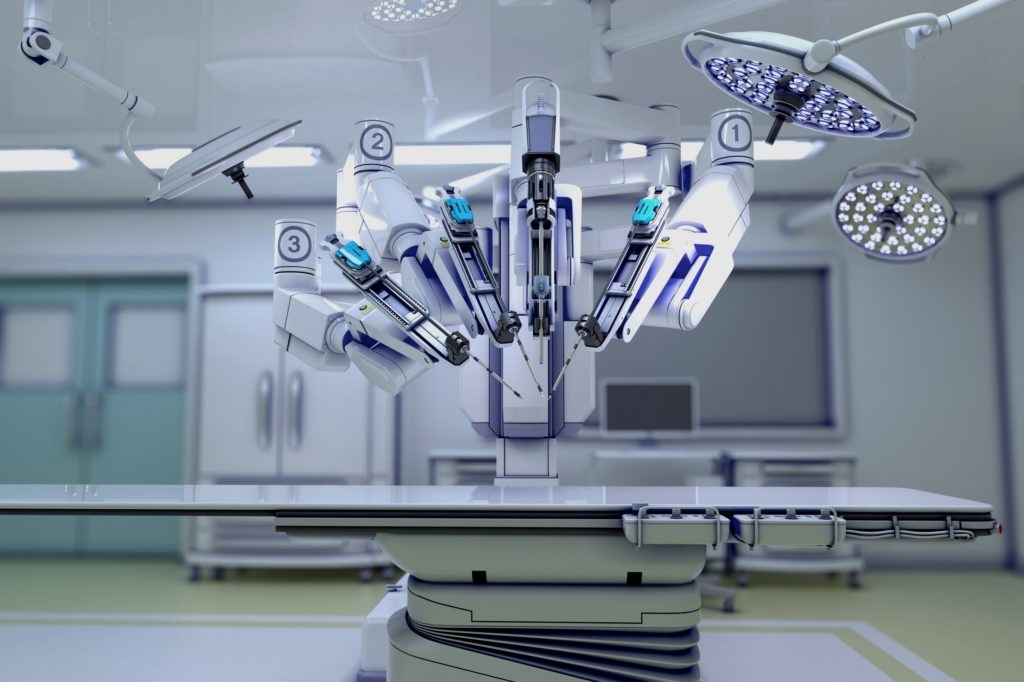
A surgical robot is an example of a force-feedback application. Source: maxon
GPX UP gearheads available now
Ultra Performance GPX gearheads are already available from maxon in 22, 32, and 42 mm diameters. Like all of the company’s “X-series” products, they are can be customized and ordered online. Currently, maxon-Sexau is working on the launch of 8 and 10 mm-diameter gears. maxon said it plans to expand the product series to a full range of 8 to 58 mm diameters.
“In summary, the new GPX UP planetary gearbox provides breakthrough improvements to higher power and continuous/peak torque output, unsurpassed efficiency, unrivaled service life, less heat generation or cooler running, as well as, true smooth back drivability — even in a multistage gearhead,” said maxon.
Tell Us What You Think!